
The LMT100 is based upon the magnetostrictive principle.
- The device electronics generates a low energy current pulse at fixed intervals.
- The electrical pulses create a magnetic field which travels down a specialized wire inside the sensor tube.
- The interaction of the magnetic field around the wire and the magnetic float causes a torsional stress wave to be induced in the wire. This torsion propagates along the wire at a known velocity, from the position of the magnetic float and toward both ends of the wire.
- A patented sensing element placed in the transmitter assembly converts the received mechanical torsion into an electrical return pulse.
- The microprocessor-based electronics measures the elapsed time between the start and return pulses (Time of Flight) and converts it into a position measurement which is proportional to the level of the float.
LMT100 is preferred for:
- Interface Measurement
- Exceptional performance with emulsion
- Measurement with foam on layers fluid surface
- Hydrocarbons and chemical control
Features
- High accuracy: 0.01% of full scale or + 1.27mm
- Never requires re-calibration: set it & forget it
- Superior Sensor (Patent #5,473,245)
- Local indication with HMI display
- Dual compartment housing with separate field terminal compartment
- Loop powered to 22m (75ft) probe length
- Total and/or interface level measurement
- Pressure to 165.48 bar (2400 psig) Std. 124.1 bar (1800 psig)
- Temperature range: -195.5 to 426.6°C (-320 to 800°F) with options
- Field replaceable/upgradable electronics module
- Built-in RFI/EMI filter
- Digital communications
Options
- Two level indications
- RTD for process temperature measurement
- Glass viewing window
- 316/L Stainless Steel enclosure
- 21-point linearization table
Torsional wave sensor
ABB, K-TEK‘s patented torsional wave sensor is constructed so that it only responds to torque. This design achieves a voltage from the sensor when the torsional stress wave is detected and
ignores all longitudinal vibrations. The sensor provides a maximum transfer of the torsional energy and provides self-cancellation of most other vibration influences. The result is an extremely high signal to noise ratio which allows our customers to use the magnetostrictive transmitter in extreme applications. The patented sensor allows for longer lengths and a wider range of temperatures and pressures.
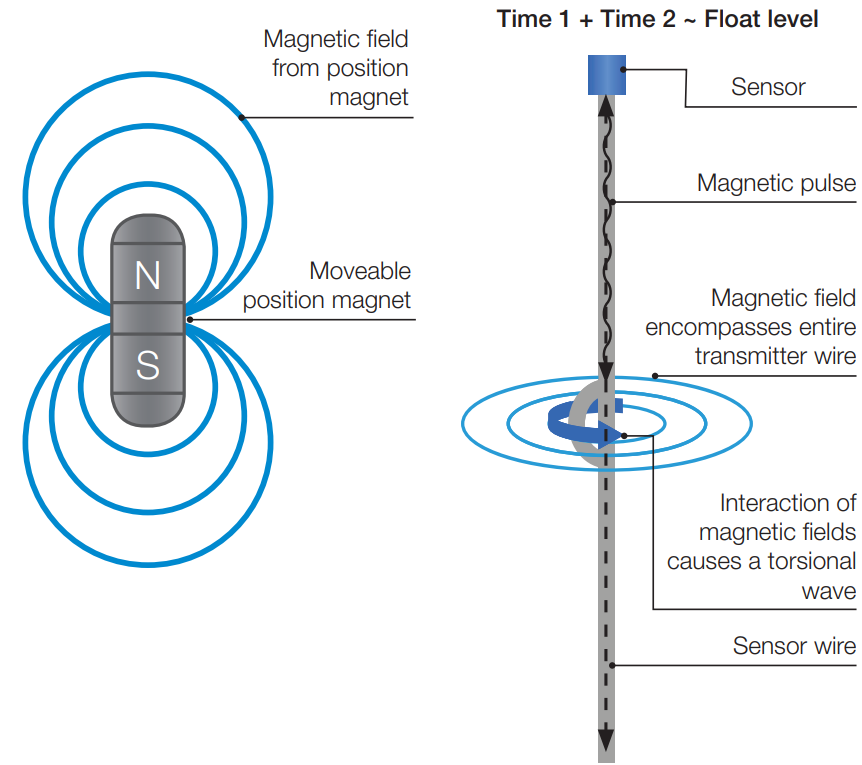